Processen
Laskennis opgefrist 2
Het booglassen met beklede elektroden
Gepubliceerd op 6-01-2019
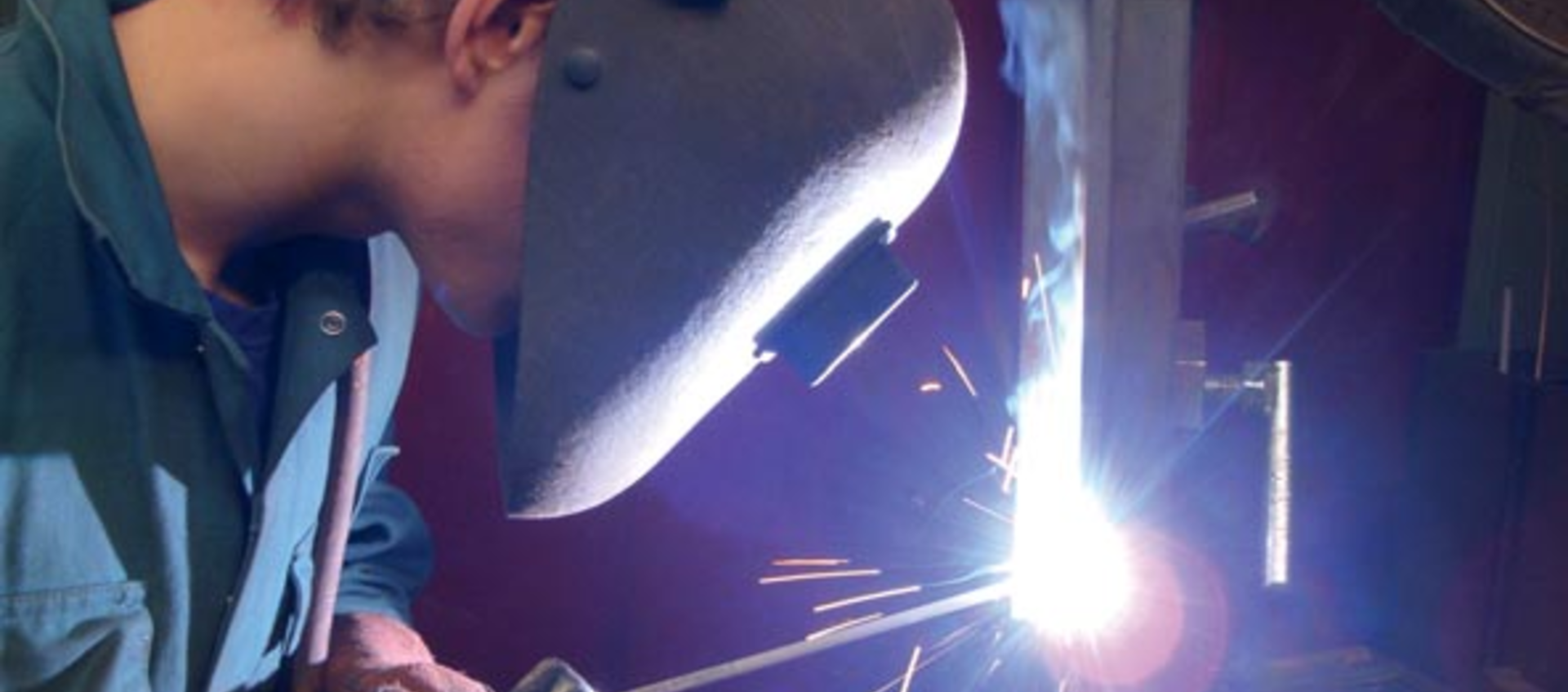
Het booglasproces met beklede elektroden bestaat al meer dan honderd jaar, maar is continu verder ontwikkeld en verbeterd. De samenstelling van de bekleding is bepalend voor de laseigenschappen.
Een stukje geschiedenis
Het lassen met een elektrische boog is in 1801 ontdekt door Sir Humphrey Davy. In 1881 ontwikkelde Auguste de Meritens een booglasapparaat met koolstofelektroden voor het lassen van loodplaten voor accu’s. De Russen Bernardos en Olszewski plaatsten de koolstofelektrode in een geïsoleerd handvat, waar ze in 1887 patent op kregen. Dit was in principe de doorbraak voor het elektrisch lassen. Charles Coffin patenteerde in 1889 het idee om de koolstofelektrode te vervangen door een metalen staaf. De lassen waren echter hard en bros. Het gebruikte staal in die tijd liet veel te wensen over en was niet te vergelijken met de kwaliteiten die we nu toepassen. De verontreinigingen en het relatief hoge koolstofgehalte gaven aanleiding tot porositeit en scheuren in de overgang. De porositeit was ook een gevolg van het ontbreken van een beschermgas of slakbescherming. In 1907 bedekte Oscar Kjellberg de metalen staaf met een dunne bekleding, bestaande uit mineralen en enkele organische stoffen. Het gevolg was een stabielere boog en een bescherming van het lasbad door de ontwikkelde gassen uit de bekleding en door de gevormde slak op het smeltbad. Dit was een wezenlijke verbetering, die werd opgevolgd door een reeks van andere procesverbeteringen.
Elektrodeproductie
De productie van de beklede elektrode was vroeger niet eenvoudig en zeer bewerkelijk. Aanvankelijk werd elke elektrode met de hand gemaakt. IJzeren staafjes werden in een pasta ondergedompeld en aan een rek opgehangen om te drogen. Als de bekleding van de elektrode door het verticaal ophangen een beetje uitzakte of niet rond werd, dan moest men dit met schuurpapier weer herstellen. Alles werd een stuk eenvoudiger toen in 1927 de fabricage van elektroden door extrusie mogelijk werd. Het is nu mogelijk om in de kleine diameters een perssnelheid te halen van meer dan 1200 stuks per minuut. (Deze snelheid is wel sterk afhankelijk van het type elektrode dat men maakt.)
Procesprincipe
Als de elektrodehouderkabel en de werkstukkabel zijn aangesloten op het lastoestel, dan gaan de elektrode en het werkstuk fungeren als anode en kathode (+pool en -pool). De ontsteking van de lasboog vindt plaats door kortsluiting van de anode met de kathode, en wel zodanig, dat op een relatief klein oppervlak een hoge stroomdichtheid ontstaat. De daardoor ontstane hoge temperatuur zorgt voor het ioniseren van de metaalatomen. De boog ontstaat zodra de elektroden op enige afstand van elkaar worden gebracht. De mate waarin de kathode elektronen kan uitstoten en de boogatmosfeer geïoniseerd kan worden, zijn bepalend voor het gedrag van de boog. De warmte van de boog laat een deel van het werkstuk en de elektrode (met de bekleding) smelten. De bekleding vormt slak die het smeltbad afschermt van de atmosfeer. De gestolde slak moet verwijderd worden voor het aanbrengen van de volgende lasrups en als de las klaar is. Omdat er steeds een nieuwe elektrode nodig is, kunnen er alleen korte stukken achter elkaar gelast worden. Het resultaat van de las is afhankelijk van de vaardigheid van de lasser.
Typen elektroden
Cellulose elektroden
Deze typen hebben in de bekleding een hoog gehalte aan cellulose. Het gevolg hiervan is een fel spuitende boog die een diepe inbranding veroorzaakt in relatief korte tijd, waardoor hoge lassnelheden kunnen worden bereikt. De cellulose veroorzaakt veel rook en spatten. Cellulose elektroden worden toegepast als grondlaag en tweede laag bij het lassen aan pijpleidingen. Deze wijze van lassen vraagt om bijzonder vakmanschap. Ook in de scheepsbouw wordt dit type toegepast. De elektrode is relatief ongevoelig voor roest, overbrugt grote vooropeningen, en is uitstekend te gebruiken in de verticaal neergaande positie.
Rutiel elektroden
Rutiel elektroden bevatten in de bekleding een hoog ge- halte aan rutiel (TiO2) en siliciumoxide (SiO2). De lasboog is relatief zacht en er ontstaan minder spatten. De elektrode ontsteekt gemakkelijk en het lasmetaal vloeit goed aan. Dit is een groot voordeel als de constructie op vermoeiing wordt belast. Vergeleken met een cellulose elektrode is de inbranding kleiner. Rutiel elektroden zijn verkrijgbaar voor alle lasposities, zowel voor wisselstroom als voor gelijkstroom. De elektrode wordt in de praktijk vooral toegepast voor het vullen van naden en voor het vervaardigen van hoeklassen. Voor deze toepassingen wordt aan de elektrode ijzerpoeder toegevoegd om het rendement te verhogen.
Basische elektroden
Basische elektroden hebben in de bekleding een hoog gehalte aan krijt (calciumcarbonaat) en vloeispaat (calciumfluoride). Deze stoffen hebben een sterk reinigende werking op het smeltbad, waardoor een zuiver, schoon lasbad verkregen wordt, zonder een hoog gehalte aan ongewenste gassen. Dit verbetert de mechanische eigenschappen aanzienlijk, in het bijzonder de kerftaaiheid. De lasbaarheid is vergeleken met een rutiel elektrode minder goed. Men moet lassen met een korte boog. De las geeft een grove tekening en bij verkeerd gebruik kunnen gemakkelijk inbrandkerven ontstaan. De slaklossing is minder goed dan bij een rutiel elektrode. Door de chemische samenstelling van de bekleding en een speciale behandeling van de elektrode kan men een lasmetaal verkrijgen met een zeer laag waterstofgehalte. Er zijn basische elektroden verkrijgbaar met een waterstofgehalte van < 5 ml/100 gram neergesmolten lasmetaal. Voor speciale toepassingen zijn er zelfs elektroden op de markt met een waterstofgehalte van < 3 ml/100 gram neergesmolten lasmetaal. Dit geeft enorme voordelen bij het lassen van staalsoorten en constructies die gevoelig zijn voor waterstofscheuren. Door vacuüm verpakken kan het lage waterstofgehalte van de elektrode over een lange tijd worden gegarandeerd.
Samengevat:
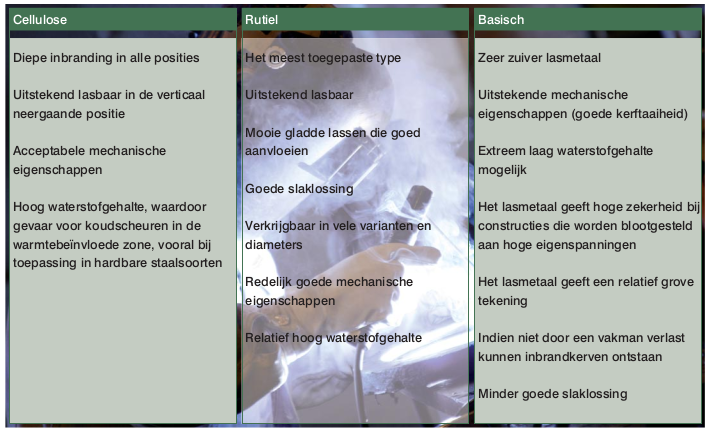
Elektroden met verhoogd rendement
Zowel bij rutiel als bij basische elektroden kan toevoeging van ijzerpoeder het rendement verhogen tot 120 à 240 %. Het rendement wordt berekend door het gewicht van het neergesmolten lasmetaal te delen door het gewicht van de verbruikte kerndraad en dit met 100 te vermenigvuldigen. Elektroden met verhoogd rendement worden toegepast voor het vullen van naden en het leggen van hoeklassen. De elektroden worden meestal slepend verlast, zijn zeer economisch en aantrekkelijk voor de lasser.
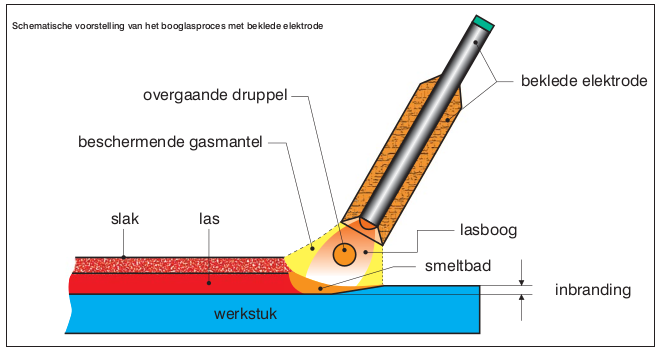
Lasapparatuur
De meeste elektroden zijn geschikt voor zowel gelijkstroom als wisselstroom, met uitzondering van (vooral basische) varianten die specifiek voor gelijkstroom zijn ontwikkeld. De voor wisselstroom ontwikkelde elektroden laten zich bijna allemaal ook uitstekend op gelijkstroom lassen. De lasapparatuur voor het booglassen met beklede elektroden is de laatste decennia aanmerkelijk kleiner en lichter geworden door toepassing van de invertertechnologie. De toepassing op montage wordt hierdoor vergemakkelijkt. Deze lasapparatuur kan relatief eenvoudig worden uitgebreid voor andere processen door het monteren van modules voor het MIG/MAG- en het TIG-lassen.
Stroomsterkte
De toe te passen stroomsterkte is afhankelijk van de kerndraaddiameter en het rendement van de elektrode. Bij een normale elektrode, zonder hoogrendement, kan men ca. 40 A per mm doorsnede aanhouden als lasstroom. Voor een elektrode met een kerndraaddiameter van 4 mm wil dit zeggen zo’n 160 A. In de praktijk worden waarden gebruikt tussen de 140 en 180 A.
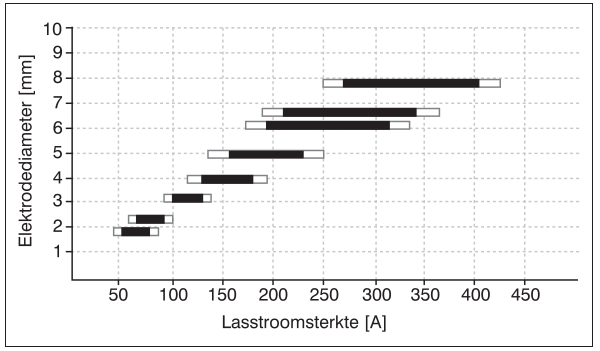
Bijlage
Download bestand
Download Laskennis_opgefrist_02_-_booglassen_met_beklede_elektroden.pdf (0 Mb)Zie ook
Gerelateerde content
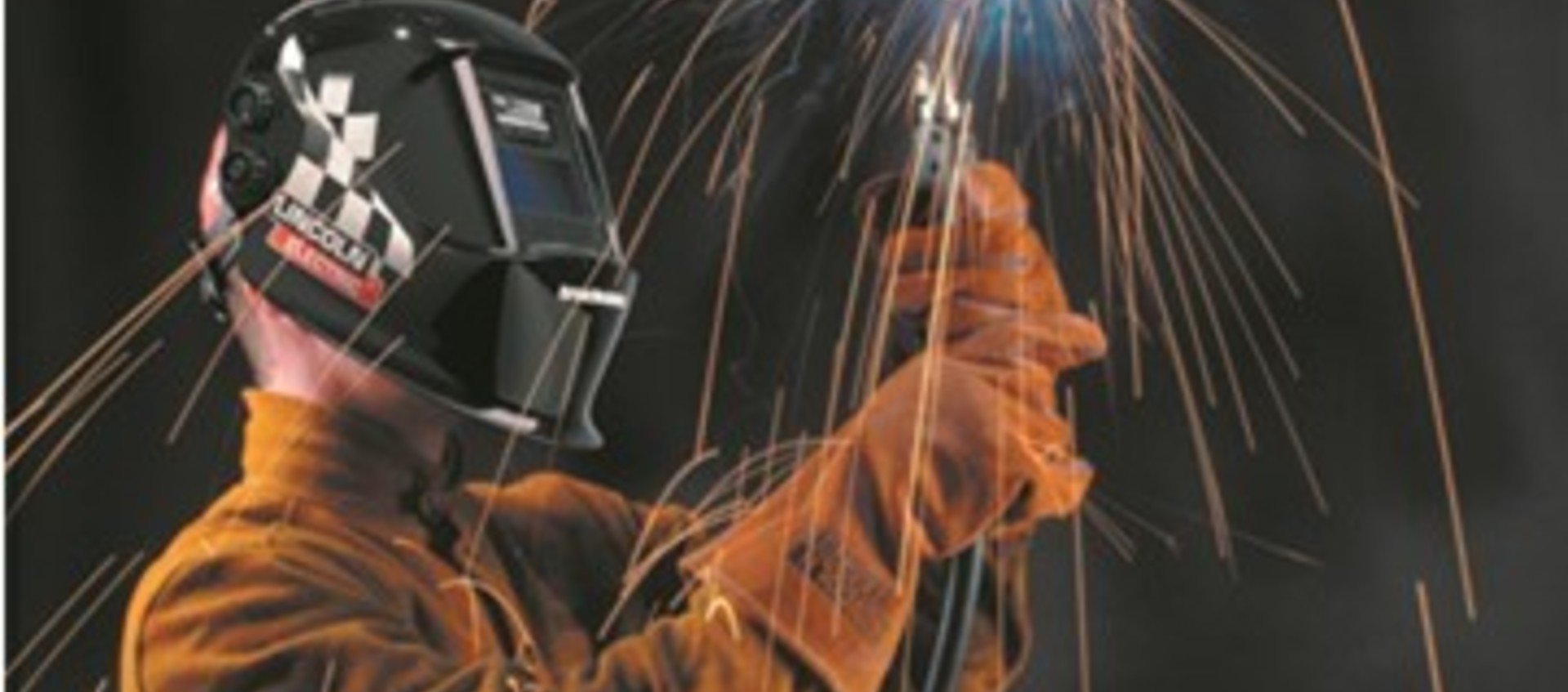